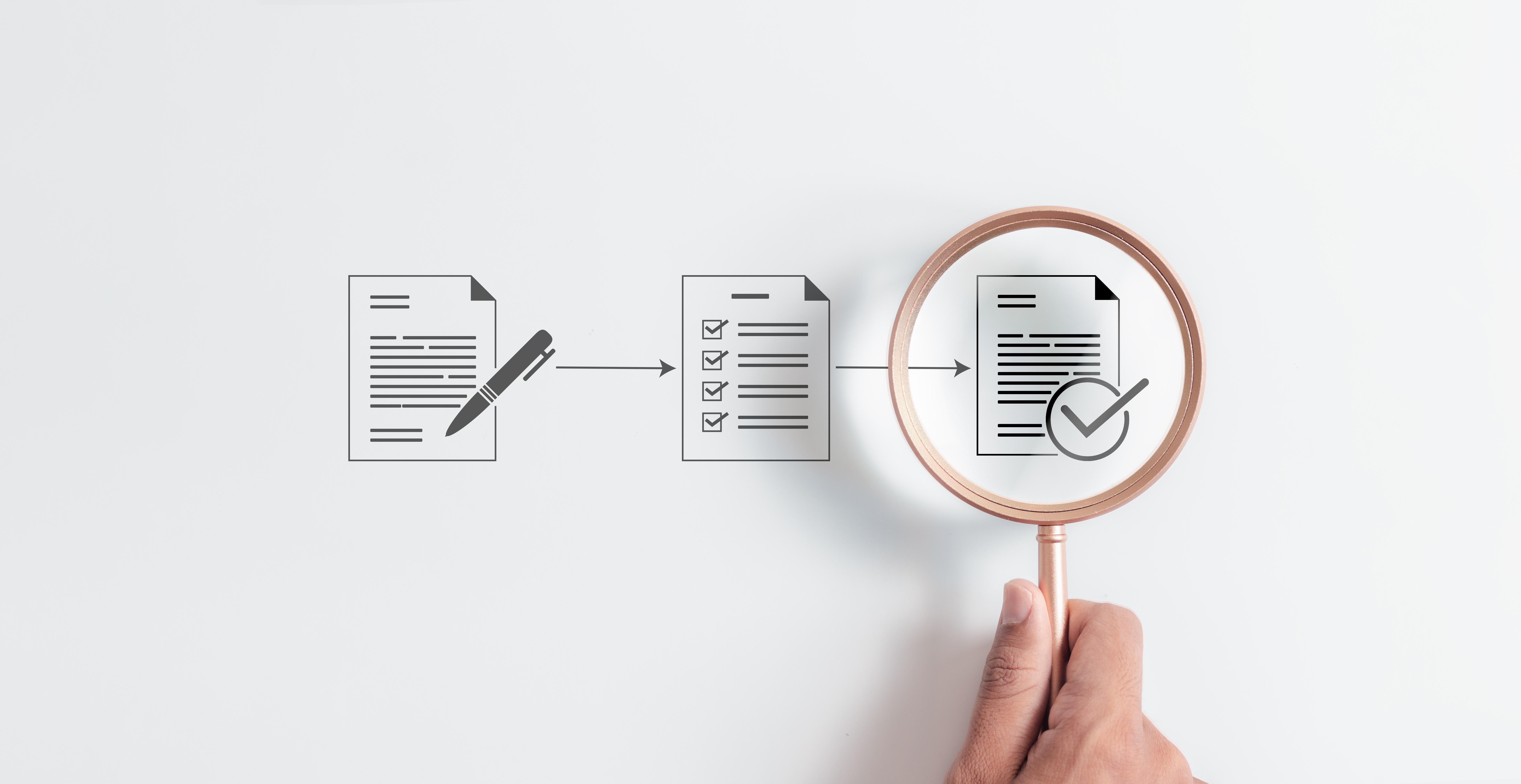
What is a cleanroom and how is it graded?
Written by Ryan
In today’s world, where precision and cleanliness are paramount, the concept of a cleanroom has become indispensable across various industries. Cleanrooms are controlled environments designed to minimise particulate contamination and maintain strict temperature, humidity, and pressure levels. These specialised rooms are utilised in sectors such as pharmaceuticals, electronics manufacturing, biotechnology, and aerospace, where even the smallest particle can cause catastrophic effects.
The primary purpose of a cleanroom is to create an environment where the concentration of airborne particles is meticulously regulated to meet specific cleanliness standards. To achieve this, cleanrooms are equipped with high-efficiency particulate air (HEPA) or ultra-low penetration air (ULPA) filtration systems that continuously circulate and purify the air. Additionally, personnel entering cleanrooms must adhere to strict protocols, including wearing specialised garments such as coveralls, gloves, masks, and shoe covers, to minimise the introduction of contaminants.
Cleanrooms come in various classifications, ranging from Class 1 (the most stringent) to Class 9 (the least stringent), based on the maximum allowable concentration of particles per cubic meter of air. Each classification is tailored to the specific requirements of the industry and the processes being performed within the cleanroom. Furthermore, cleanroom designs incorporate seamless surfaces, smooth flooring, and advanced monitoring systems to maintain cleanliness and ensure compliance with industry standards and regulations.
In essence, cleanrooms play a pivotal role in safeguarding product quality, optimising manufacturing processes, and protecting sensitive materials from contamination. As technology advances and industries demand ever-higher levels of precision and purity, the importance of cleanrooms in maintaining cleanliness and controlling environmental factors cannot be overstated. Whether it’s producing life-saving pharmaceuticals or manufacturing cutting-edge semiconductor chips, cleanrooms remain the cornerstone of modern industrial operations, ensuring that quality and reliability are upheld to the highest standards.
Cleanrooms are classified according to international standards set by the International Organization for Standardisation (ISO). These standards define the maximum allowable concentration of particles per cubic meter of air for different particle sizes. The ISO classification system assigns cleanrooms a numerical grade, which correlates with the level of cleanliness and the specific industry requirements. Let’s delve deeper into the ISO grades for cleanrooms:
- ISO 1 to ISO 9: The ISO classification system ranges from ISO 1 (the most stringent) to ISO 9 (the least stringent). Each classification corresponds to a maximum allowable concentration of particles per cubic meter of air for particles of a specific size. For example, ISO 1 cleanrooms permit no more than 10 particles of 0.1 micrometers or larger than per cubic meter of air, while ISO 9 cleanrooms allow up to 35,200,000 particles of 0.5 micrometers or larger per cubic meter of air.
US209E has been superseded by ISO 1644, only shown above for reference.
- Applications and Requirements: Different industries have varying cleanliness requirements, which dictate the ISO class of cleanroom needed. For instance, industries such as semiconductor manufacturing and nanotechnology typically require ISO 1 to ISO 3 cleanrooms to prevent even minute particle contamination. In contrast, industries like pharmaceuticals and biotechnology may operate with ISO 5 to ISO 8 cleanrooms, where a higher particle count is permissible but still tightly controlled.
- Design and Operation: Achieving and maintaining the specified ISO class requires meticulous design, construction, and operation of the cleanroom. Factors such as lighting, airflow, filtration, room pressurisation, and personnel protocols play critical roles. HEPA or ULPA filters are essential components, along with stringent gowning procedures for personnel entering the cleanroom.
- Continuous Monitoring and Maintenance: Cleanrooms must undergo regular monitoring and maintenance to ensure they adhere to the specified ISO class. Continuous monitoring of air quality, temperature, humidity, and pressure is essential to detect any deviations from the required standards promptly. Additionally, routine cleaning and filter replacement are necessary to sustain optimal cleanliness levels and prevent contamination.
EU GMP: The European Union (EU) Good Manufacturing Practice (GMP) guidelines for pharmaceutical manufacturing establish strict standards to ensure the quality and safety of medicinal products. These guidelines outline different “Grades” for cleanrooms, which are classified based on the level of cleanliness and environmental control required during various stages of drug production. The four primary GMP Grades in the EU are Grade A, B, C, and D.
In conclusion, understanding the ISO grades for cleanrooms is crucial for industries that rely on controlled environments to maintain product quality and integrity. Adhering to these standards ensures that cleanrooms meet the stringent cleanliness requirements demanded by various industries, ultimately safeguarding product reliability and consumer safety.
EU GMP explained can be found https://www.solite-europe.com/informative/eu-gmp-explained/